Stress in physics acts as a gauge for the strength of the forces that lead to deformation. Stress is typically described as force per unit area. Tensile stress occurs when forces act on something and make it elongate, like when an elastic band is stretched. Similarly, When an object is compressed by forces, compression stress results. Bulk stress, also known as volume stress, develops when an item is compressed from all sides, such as a submarine submerged in the water. When two materials glide over or against one another, shear stress results.
The SI unit of stress is the pascal (Pa). When one newton of force presses on a unit surface area of one meter squared, the resulting stress is one pascal:
One pascal=1N/m2
Table of Contents
Stress Units
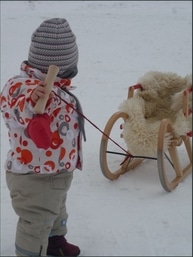
- Pascal (One pascal equals N/m2)- SI derived units
- Pound per square inch (lb/in2)- US unit
- Atmosphere (1 atm = 14.7psi)
Concept of Strain
Stress causes an object or medium to deform. This deformation can be quantified by the term “strain.” When under tensile, bulk, or shear stress, the expression of strain is a fractional change in length, volume, or shape.
The term “strain is a number without any dimensions. Important examples are tensile strain, bulk strain and shear strain. Tensile strain is a strain caused by tensile stress. Bulk strain, also known as volume strain, is a strain brought on by shear stress, while shear strain is a strain brought on by shear stress.
In the linear limit of low-stress values, the general relation between stress and strain is
Stress = (elastic modulus) Strain
Since strain has no dimensions, stress and the elastic modulus share the same physical unit.
Stress has a negligible impact on an object with a high elastic modulus value. A low elastic modulus, on the other hand, denotes significant strain and deformation brought on by stress.
Young’s modulus is the term for the elastic modulus for tensile stress; bulk modulus is the term for the elastic modulus for bulk stress; and shear modulus is the term for the elastic modulus for shear stress.
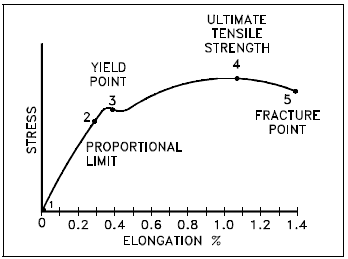
Daily Life Examples of Stress in Physics
In physics, stress can refer to the force per unit area exerted on an object, which can cause it to change its shape or deform. There are several different types of stress that can be experienced by an object, including:
- Tension stress is caused when an object is stretched or tugged, causing it to elongate. Ropes and wires are frequently subjected to this type of strain.
- Compression stress is caused when an object is squeezed or compressed, causing it to shorten. This type of tension is frequent in springs and beams.
- Shear stress arises when two opposed forces are applied to an item in opposite directions, causing it to deform by sliding or shearing. Torsionally stressed materials typically suffer this form of stress.
- Bending stress: This occurs when an object is subjected to a bending moment, causing it to deform into a curved shape. This type of stress is commonly experienced by beams and other structures that are subjected to loads that cause bending.
- Torsional stress occurs when an object is twisted, causing it to deform into a helical pattern. Shafts and other objects subjected to rotational loads frequently encounter this form of stress.
Hook’s Law
Hooke’s law is critical for understanding how a material behaves when stretched or squeezed.
Hooke’s law asserts that strain is proportionate to applied stress within a material’s elastic limit. When elastic materials are stretched, the atoms and molecules deform until tension is applied, and then they return to their former state when the stress is released.
Yield Point
On a stress-strain curve, the yield point denotes the end of elastic behavior and the beginning of plastic behavior. The yield strength, also known as yield stress, of a material is the stress at which it begins to bend plastically, whereas the yield point is the point at which nonlinear (elastic + plastic) deformation occurs. When the applied force is withdrawn, the material deforms elastically before the yield point and returns to its former shape. After reaching the yield point, a portion of the deformation becomes permanent and irreversible.
Fracture Point
The fracture point is the point where the material physically breaks as a result of strain. Even though the related stress is less than the ultimate strength, the strain reaches its maximum value at this point, and the material splits
Limit of Proportionality
The limit of proportionality specifies the point beyond which Hooke’s law no longer holds true when stretching a material. The elastic limit of a material is the farthest distance it can be stretched or bent before returning to its original shape.
Definition of True Stress, True Strain, Engineering Stress, and Engineering Strain
- Engineering stress is computed by dividing the applied load by the initial cross-sectional area of a material. Nominal stress is another word for nominal stress.
- True stress is defined as the applied load divided by the specimen’s genuine cross-sectional area (the changing area with respect to time) at that load.
- Engineering strain is the amount a material deforms per unit length in a tensile test. Engineering strain is also known as nominal strain.
- True strain is equal to the natural log of the quotient of current length over original length.
Engineering stress | σ = Load/cross-sectional area of the specimen before deformation has taken place |
True stress | σ = cross-sectional area of specimen at which the load is applied |
Engineering strain | ε = total elongation/original value of the gage length |
true strain | εt =ln{(successive values of the length as it changes)/original value of the gage length} |
Summary
- Stress is defined as force per unit area and represents the magnitude of the forces that induce deformation.
- Strain describes the distortion of a substance as a result of applied stress.
- Strain is a number with no dimensions.
- Because strain has no dimensions, the elastic modulus has the same physical unit as stress.
Related Links
Strain Energy Concept And Formula Derivation
Flexural Strength- An Overview
Linear Motion or Rectilinear Motion
The Spring Constant – Hooke’s Law
Can Work Be Negative?
Mechanical Energy Formula & Examples
Frequently Asked Questions
1. What is meant by stress in physics?
In physics, stress is defined as the amount of force applied to an item divided by the cross-section area of the object on which the force operates.
2. What are the three types of stress in physics?
Tensile, compressive, and shear stresses are the three basic types of stress in physics.
3. Is stress a vector?
The stress quantity is neither a scalar nor a vector quantity. It is a tensor quantity as stress equals the amount of the internal reaction force divided by the cross-sectional area,
4. What is the difference between stress and pressure?
Internal resistive force to deformation per unit area is described as stress. The amount of force applied per unit area is known as pressure.
5. Is stress a tensor?
A tensor is a quantity with magnitude, direction, and a plane in which it acts, such as stress or strain. Both strain and stress are tensor quantities.
6. Is the tension and stress the same in physics?
Tensile stress (also known as tension) is a type of stress that causes a material’s length to grow in the tensile direction. The material’s volume remains constant. When two equal and opposite forces are applied to a body, the resulting tension is known as tensile stress.
7. Briefly define conduction in physics?
Conduction in physics refers to the transfer of energy via the movement of particles in contact with one another.
8. What is the difference between Tensile Stress and Compressive Stress?
The main difference between tensile and compressive stress is that tensile tension causes elongation while compressive stress causes shortening. Some materials are strong when subjected to tensile stress yet weak when subjected to compressive stress.
More Links
What is a Biochip?| A Short Overview
Work-Energy Theorem
Light Energy Definition
Energy Stored in a Capacitor
Work-Formula, Definition, & Units
Thermal Diffusivity
- BCl3 Lewis Structure in four simple steps - November 1, 2023
- PH3 Lewis Structure in four simple steps - October 8, 2023
- PF3 Lewis structure in four simple steps - September 24, 2023