Mechanical stress and strain are fundamental concepts in the field of materials science and engineering that describe how materials respond to external forces.
Mechanical stress refers to the internal forces or pressure exerted on a material when an external force is applied. It is defined as the force per unit area acting on a material. Stress is typically measured in units of force divided by area, such as pounds per square inch (psi) or pascals (Pa). When a material is subjected to stress, it experiences internal deformations or changes in shape. The formula for mechanical stress is:
Stress (σ) = Force (F) / Area (A)
Where:
- Stress (σ) is the mechanical stress experienced by the material (measured in units of force divided by area, such as Pascals or PSI).
- Force (F) is the applied force acting on the material.
- Area (A) is the cross-sectional area of the material that is perpendicular to the direction of the applied force.
Mechanical strain, on the other hand, measures the amount of deformation or change in shape that occurs in a material when subjected to stress. It is a dimensionless quantity and is usually expressed as a ratio or percentage. Strain is determined by dividing the change in length or shape of a material by its original length or shape. Tensile or Compressive Strain formula is given as:
Strain (ε) = Change in Length (ΔL) / Original Length (L)
Where:
- Strain (ε) represents the tensile or compressive strain (dimensionless).
- Change in Length (ΔL) is the difference between the final length and the original length of the material.
- Original Length (L) is the initial length of the material.
Table of Contents
Daily Life Examples of Stress and Strain
- Stretching a Rubber Band: When you stretch a rubber band, you apply mechanical stress to it. The rubber band experiences an increase in length, and the internal forces within the rubber band create strain. When you release the rubber band, it returns to its original shape, exhibiting elastic behavior.
- Bending a Metal Wire: If you take a thin metal wire and bend it, you apply stress to the wire. The wire undergoes deformation and experiences strain. The extent of bending determines the magnitude of strain, and the wire may exhibit plastic behavior if it doesn’t return to its original shape after bending.
- Compression of a Spring: When you compress a spring, you exert a compressive stress on it. The spring undergoes deformation and experiences strain as it gets compressed. The spring stores potential energy in its deformed state and can release it to bounce back when the compressive stress is removed.
- Sitting on a Chair: When you sit on a chair, both you and the chair experience mechanical stress and strain. The chair’s structure bears your weight, and the materials it is made of undergo deformation and strain. The chair needs to be designed to handle the stress and strain to ensure stability and durability.
- Tension in a Rope: If you pull on a rope, it experiences tensile stress. The rope stretches and undergoes strain. The amount of stretching and strain depends on the force applied. Rope used in activities like rock climbing or towing needs to withstand significant stress without breaking.
Relationship between Stress and Strain
The relationship between stress and strain is described by the material’s mechanical properties, such as its stiffness, elasticity, and strength. Different materials exhibit different responses to stress and strain. Some materials, like metals, can deform significantly under stress and then return to their original shape when the stress is removed, showing elastic behavior. Other materials, like plastics, may experience permanent deformation even after the stress is removed, exhibiting plastic behavior.
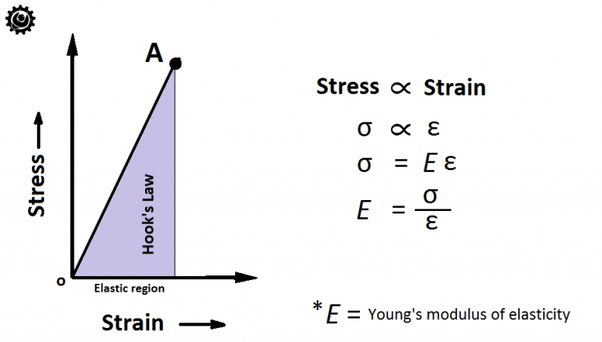
Types of Stress
Types of Stress | Description |
Tensile Stress | Occurs when forces pull a material apart |
Compressive Stress | Results from forces squeezing or compressing a material |
Shear Stress | Arises from parallel forces causing material layers to slide |
Bending Stress | Occurs when a material is bent or flexed |
Torsional Stress | Caused by twisting forces acting on a material |
Types of Strain
Types of Strain | Description |
Tensile Strain | Elongation or extension of a material in the direction of stress |
Compressive Strain | Decrease in length or volume of a material due to compressive stress |
Shear Strain | Angular deformation resulting from shear stress |
Bending Strain | Change in shape or curvature of a material due to bending stress |
Torsional Strain | Twist or change in orientation of a material under torsional stress |
Stress-Strain Formulas
Strain Formula | Variables Explanation | Examples |
Tensile Stress | σ = F/A: Force applied per unit area | Pulling on a rope, stretching a rubber band |
Tensile Strain | ε = ΔL/L: Change in length divided by original length | |
Compressive Stress: | σ = F/A: Force applied per unit area | Compressing a spring, pressing on a foam block |
Compressive Strain: | ε = ΔL/L: Change in length divided by original length | |
Shear Stress | τ = F/A: Force applied per unit area | Cutting with scissors, shearing action in metals |
Shear Strain | γ = Δx/h: Displacement parallel to applied force divided by the thickness | |
Bending Stress | σ = (M * c) / I: Bending moment times distance divided by moment of inertia | Bending a beam, flexing a diving board |
Bending Strain | ε = (y * δ) / L: Displacement times height divided by original length | |
Torsional Stress | τ = (T * r) / J: Torque times radial distance divided by polar moment of inertia | Twisting a screwdriver, rotating a shaft |
Torsional Strain | φ = θ * r: Angle of twist times radial distance |
Young’s modulus of elasticity
Young’s modulus of elasticity, represented by the symbol E, is a measure of how stiff or rigid a material is. It describes how much a material will deform when subjected to an external force. A higher Young’s modulus indicates a stiffer material that is less likely to deform, while a lower Young’s modulus indicates a more flexible material that is more prone to deformation. Young’s modulus is an important factor in engineering, helping in material selection and predicting the behavior of materials under different loads.
Symbolized by the letter “E,” Young’s modulus is defined as the ratio of tensile or compressive stress (σ) to the corresponding strain (ε) in the linear elastic region:
E = σ / ε
Where:
- E is the Young’s modulus of elasticity (measured in units of pressure, such as Pascals or PSI).
- σ is the stress applied to the material (force per unit area).
- ε is the resulting strain in the material (dimensionless).
Conclusion
Understanding the concepts of stress and strain is crucial for designing and analyzing the performance of materials and structures in various engineering applications. By studying stress and strain, engineers can predict how materials will behave under different loading conditions and ensure the safety and reliability of structures and components.
More Links
Hooke’s Law: Definition, Examples, and Applications
Resilience: Examples from Physics and Everyday Life
Elastic Modulus: Predicting Material Deformation and Failure
Flexural Strength| Simple Definition and Daily Life Examples
Strain Energy- Definition, Formula and Daily Life Examples
- BCl3 Lewis Structure in four simple steps - November 1, 2023
- PH3 Lewis Structure in four simple steps - October 8, 2023
- PF3 Lewis structure in four simple steps - September 24, 2023